The garden wall was delayed into the winter while a tree stump was removed and it’s getting warm enough to avoid bad frosts now. I spent a day figuring out levels and worked out that a 450mm * 450mm hole would be about fine everywhere. Planning 300mm concrete then a couple of bricks up to ground level. I don’t know exactly how tall my wall will be, but guessing I’ll run out of bricks between 1.2m and 1.4m.
A man with a digger got the hole dug by lunchtime. Ripping up the old foundations made the hole a bit wider than intended.

The ground levels step down by a couple of bricks at the corner of the wall. I’ve put formers in to make the drop one brick at a time. They aren’t where I intended as it was easier to put them where there were banks either side to drive stakes into. There’s also a bit of shuttering at the side of the hole where the tree was.
The vertical stakes indicate the level of the top of the concrete which is a couple of bricks below ground level. They don’t look level in the photo as they go squint when you hit a stone, but they should be accurate for height. They all go into the ground more than 200mm which is useful as you can’t see them when the concrete is poured and they get knocked with the rake.
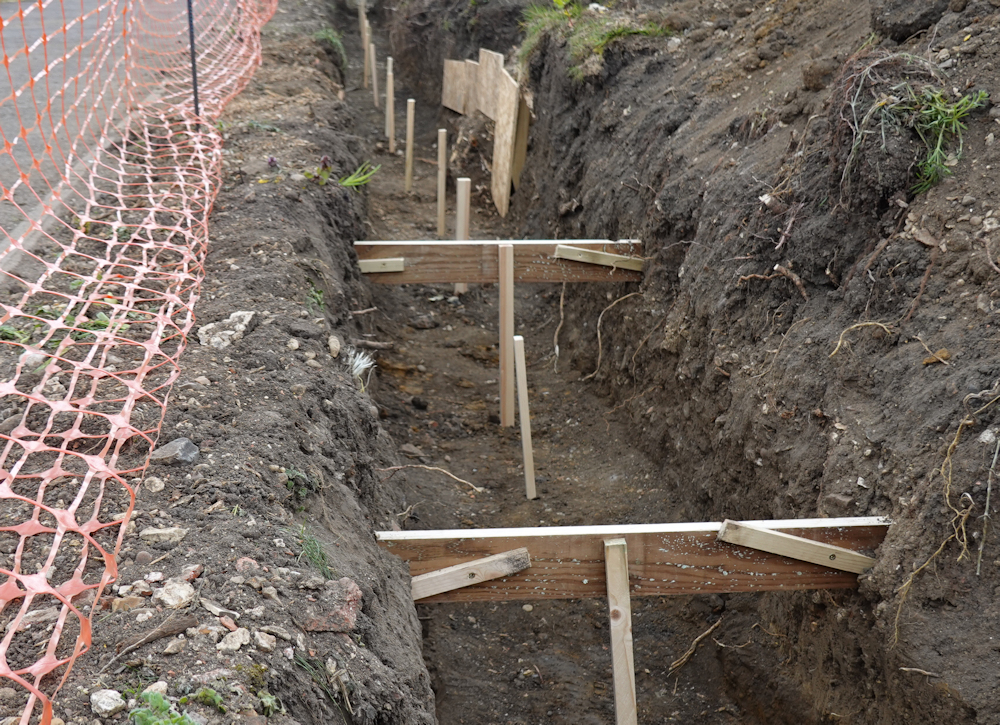
I used a mix on site concrete truck. They started off with some fairly firm concrete to dam the level changes and then filled the trench up with the normal runny concrete while I raked and tamped behind.
It’s mostly worked. The foundations start 1/8 inch high, then fall 1/4 inch low for a good length. Also one of the dams is leaking very slowly and one end has dropped by 1/2 inch. I’m hoping when the concrete gets around to it’s initial cure it will put a stop to that. We’ve been having light frosts so I’ve covered everything with hessian and can worry about it later.
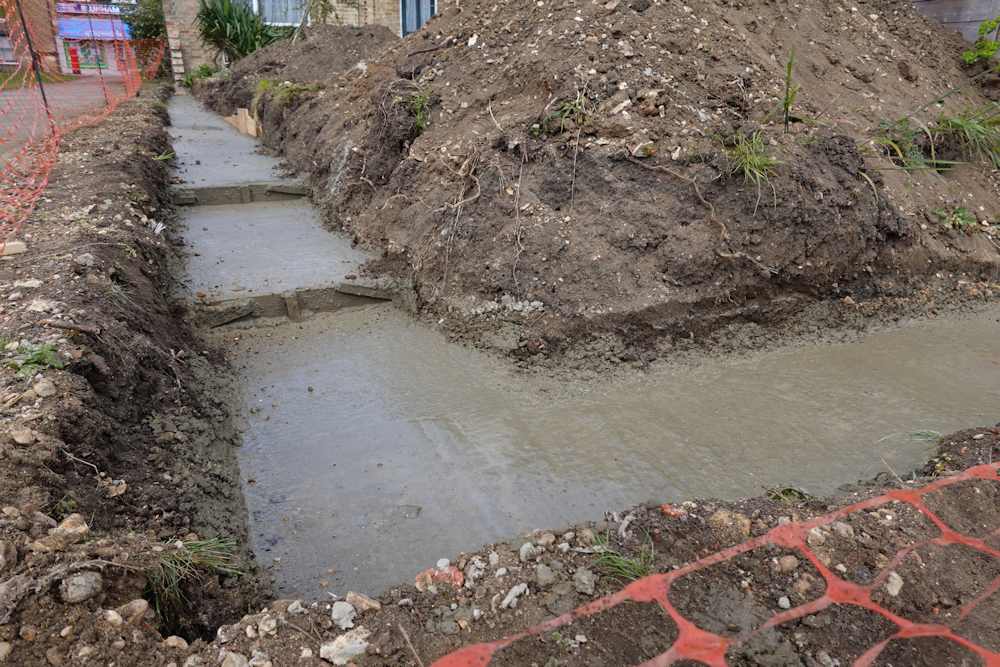
The first bricks went in a couple of days after the concrete pour. The existing wall leans a little and I didn’t have a good reference for the new wall as it starts off lower down than it used to and there is a slight change in direction. The existing wall was awful to set out from.
The cunning plan is to build a pier after these bricks. I can set the wall out nice and straight from there and also blend the old wall into the pier.
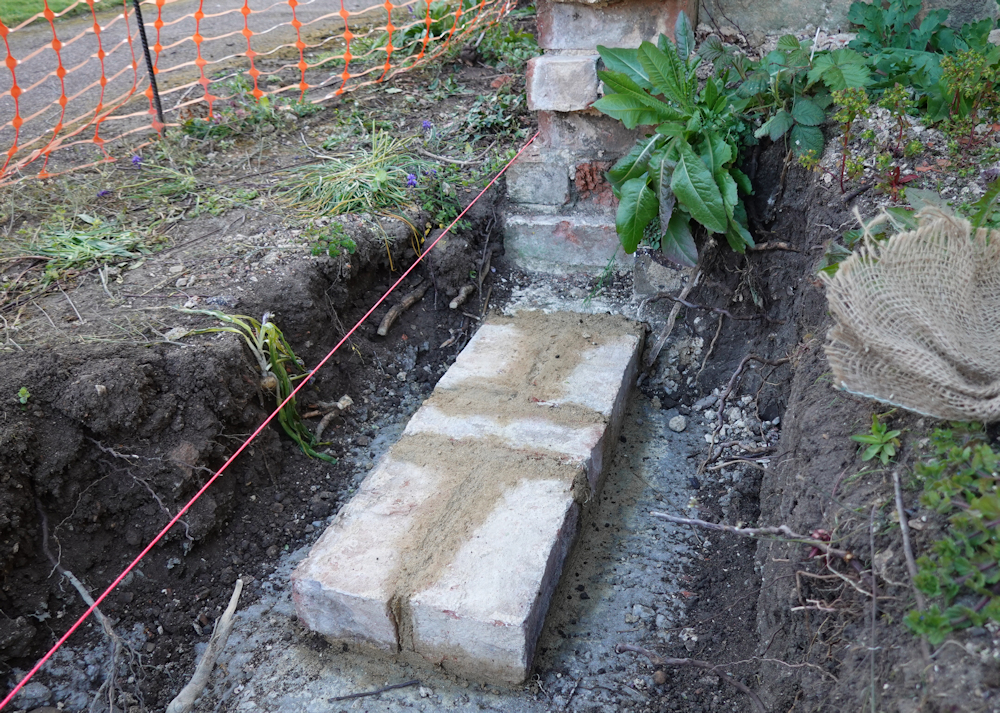